Visita aziendale in BLM Group Adige
Tra innovazione, formazione e sostenibilità ambientale
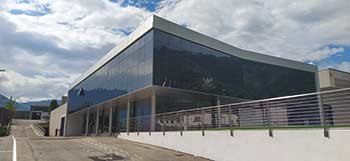
In una soleggiata giornata di metà settembre abbiamo portato i nostro soci vicino al lago di Levico per
visitare una bella realtà industriale del nostro territorio,
particolarmente dinamica, innovativa e votata alla sostenibilità.
La tradizione della meccanica affonda qui in Trentino
le radici nel secondo dopoguerra, quando negli anni
‘50 nacque la Adige Sala, azienda storica costruttrice di macchinari per la lavorazione delle lamiere, acquisita poi negli anno ‘90 dalla lombarda BLM che ha
investito fino a diventare un centro d’eccellenza nella
progettazione e costruzione di sofisticati impianti per la
lavorazione della lamiera e del tubo, investendo anche
nella ricerca e nella formazione con positive ricadute
su tutto il territorio.
All’ingresso dello stabilimento il primo impatto è di
grande modernità ed organizzazione: ci accoglie la
dott.ssa Vaccari ed assieme al direttore vendite ing. Toselli e al direttore generale dott. Luca Arighi iniziamo il nostro percorso.
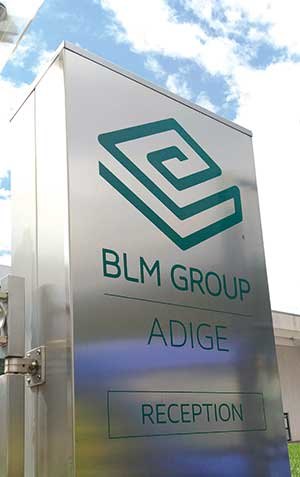
Visitiamo prima di tutto lo “show room” dei prodotti BLM group, cioè uno sterminato capannone industriale con ben ordinati tutti gli impianti di lavorazione perfettamente in funzione per soddisfare ogni curiosità dei visitatori: vediamo il taglio al laser di lamiere lunghe fino a 6 metri e con spessori di oltre 2 cm o di tubi di diametro oltre il mezzo metro; vediamo il taglio laser in 3D, cioè con qualsiasi forma di taglio su tubi formati e piegati in qualsiasi posizione; oppure sofisticate curvatubi e sagomatubi con cambi di produzione così rapidi da eliminare scarti ed avere sempre il “primo pezzo giusto”, o per finire una macchina che piega, raddrizza, taglia, smussa tubi sottili di soli 10 mm di diametro in qualsiasi posizione con estrema velocità e produttività non stop 24 / 7.
Colpisce la pulizia, la giovane età delle maestranze – che la dice lunga sulla vision aziendale – nonché la presenza di altri gruppi di visitatori ed anche di scolaresche: BLM è infatti impegnata anche nella didattica ed assieme agli studenti delle scuole locali ha realizzato progetti sulla sostenibilità e sulla raccolta differenziata automatizzata, diffondendo questa cultura già ai giovanissimi.
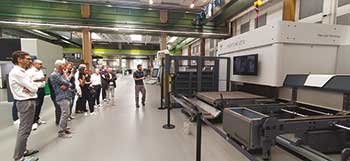
Accompagnati dal direttore di stabilimento ing. Alberto Longobardi – nostro affezionato socio e grande
esperto di Intelligenza Artificiale – visitiamo lo stabilimento produttivo vero e proprio, progettato in maniera
eco sostenibile e climatizzato con un bassissimo impatto ambientale.
Troviamo sempre grande pulizia ed organizzazione: la
superficie dello stabilimento è suddivisa in una trentina
di aree dedicate ad altrettanti macchinari in via di costruzione, dove la componentistica è realizzata da un
vasto parco di fornitori qualificati mentre qui si effettua
l’assemblaggio dei gruppi principali; il montaggio completo del macchinario con il conseguente primo – e unico – collaudo funzionale avverrà solo davanti al cliente
finale, per cui si lavora per essere certi che la riuscita
sia perfetta al 100% al primo colpo.
Questo si raggiunge con una meticolosa progettazione
al computer CAD/CAM grafico tridimensionale nato per
sfruttare ogni margine di prestazione delle macchine,
con vaste librerie di funzioni che velocizzano e semplificano la progettazione, con una stima accurata dei
tempi e dei costi di realizzazione per avere una preventivazione di dettaglio.
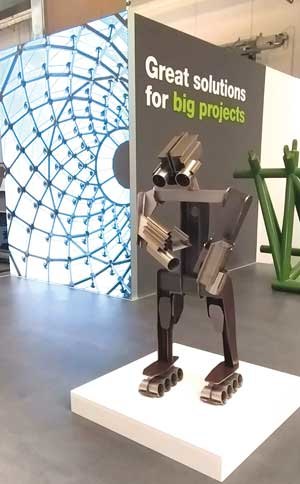
Il controllo dei tempi avviene efficacemente tramite un
monitor gigantesco all’ingresso dello stabilimento che
mostra in tempo reale l’evoluzione delle lavorazioni nelle singole aree, ed un sistema semaforico mostra quelle che rispettano i tempi, quelle a rischio oppure quelle
in ritardo che richiedono azioni correttive tempestive.
E viste le ottime performance raggiunte, si capisce che
il metodo funziona!
Per chiudere ci è stato mostrato il magazzino dei semilavorati completamente automatizzato che preleva
e trasporta il componente fino all’area che lo richiede
proprio in quel momento: ovviamente si tratta di intelligenza artificiale che qui la fa da padrona, largamente utilizzata anche nella gestione della Supply Chain,
programmazione, controllo e movimentazione ottimale
della produzione in stretto e continuo dialogo tra Fornitori e Clienti.
Anche questa volta siamo arrivati a fine visita dello stabilimento un po’ storditi, davanti a tanta tecnologia e
innovazione, e piacevolmente sorpresi dall’attenzione
prestata alla sostenibilità ambientale ed alla formazione ad ogni livello per una crescita professionale e
umana della persona: come ci ha detto il dott. Arighi,
“le imprese devono essere luoghi formativi, co-protagonisti di percorsi di crescita con scuola e Università”.
Questa è l’industria 5.0.
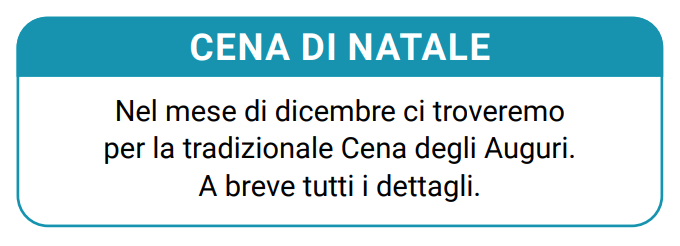
06 ottobre 2023