Pittini, visita ad una acciaieria
Visita alle Ferriere Pittini del 21 marzo
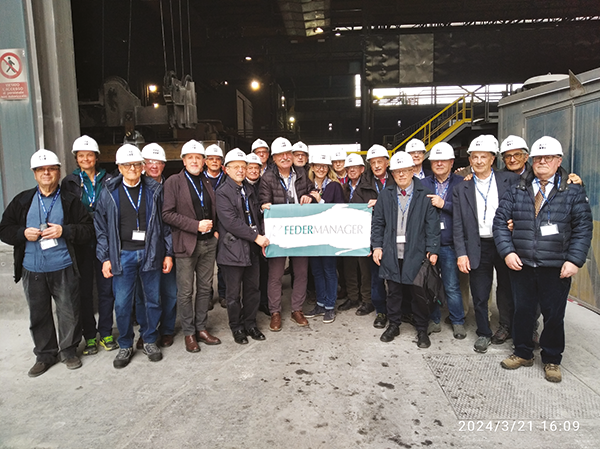
Tutto esaurito per la visita alle Ferriere Pittini del 21 marzo: i 30 posti disponibili sono stati rapidamente prenotati, lasciando qualcuno dei colleghi Federmanager in waiting list.
E in effetti la visita ad una acciaieria in piena produzione, dove l’acciaio incandescente fuso a 1600 °C viene colato dalla siviera nella lingottiera di una colata continua non è roba da perdere. Il gruppo Pittini produce circa tre milioni di tonnellate/anno di acciaio (prodotti lunghi), partendo da rottame, nei tre stabilimenti di Osoppo, Verona e Potenza: così spiega la responsabile Human Resources, Micaela Di Giusto, che ci ha accolto all’inizio della visita.
In tutto 2000 dipendenti distribuiti in 21 strutture produttive e di servizio logistico in Europa. I prodotti core dell’azienda sono i tondi in rotolo o in barre per le reti elettrosaldate utilizzate in edilizia, ma non solo. L’azienda esporta due terzi della produzione: da una parte un plus, dall’altra una complicazione perché, non esistendo una normativa europea sul prodotto, la Pittini deve diversificare i prodotti a seconda dei vari Stati: ciò ha conseguenza sui volumi dei magazzini. C’è molta attenzione sugli aspetti ESG e l’integrazione sul territorio: il fiore all’occhiello del Gruppo è rappresentato dalla Corporate School (Officina Pittini per la Formazione – OPF), che è ente accreditato come istituto formatore presso la Regione FVG ed eroga i suoi servizi non solo al proprio personale, ma anche a privati e scuole. La visita da parte di scolaresche sono quindi frequenti, ma noi di Federmanager facciamo più domande, dice ridendo la Di Giusto.
Il cuore della produzione è il forno fusorio elettrico, illustrato successivamente dal resposabile del Controllo Qualità, Martino Di Giusto. Si tratta di un grosso ‘pentolone’ del diametro di circa 7 metri, con il fondo (tino inferiore) appoggiato su una piattaforma basculante, che permette di cambiare la inclinazione del forno per le operazioni spillaggio dell’acciaio fuso. Il fondo è rivestito in materiale refrattario (magnesite e dolomite) e può contenere circa 150 ton di acciaio fuso a 1620 °C. Sopra al tino inferiore c’è una seconda parte del pentolone (tino superiore), che porta dei pannelli raffreddati ad acqua. Segue più in alto la volta (che sarebbe il coperchio del pentolone). Può essere sollevata per le operazioni di carica del rottame e presenta dei fori, attraverso i quali vengono fatti passare tre cilindri di grafite (gli elettrodi) e vengono aspirati i fumi.
Il rottame ferroso, preliminarmente controllato e selezionato, viene alimentato gradualmente nel forno tramite ceste e viene fuso finchè la capienza del forno è lentamente raggiunta: ci vogliono circa 45 minuti per un ciclo. Il riscaldamento del rottame è dovuto principalmente agli archi elettrici che si generano tra i tre elettrodi di grafite (tre cilindri che calano dalla volta, alimentati in corrente alternata) e metallo sul fondo del tino e, in minor parte, alle reazioni esotermiche che si generano nel bagno.
Dopo controlli e aggiunte varie per raggiungere la composizione desiderata, il metallo fuso viene versato in un altro pentolone, la siviera (LF), per essere poi trasportato alla postazione della colata continua. Anche in siviera la temperatura viene mantenuta alta utilizzando tre elettrodi di grafite; il metallo inoltre viene ulteriormente affinato e desolforato tramite aggiunte di ferroleghe e altro. Successivamente il metallo fuso viene versato dalla siviera nella paniera della colata continua, che suddivide il materiale in sei linee di colaggio destinate a sei lingottiere, da ognuna delle quali esce dal fondo verticalmente una billetta a sezione quadra (ca 20 cm), parzialmente solida (si forma un guscio solido), curvata e trainata successivamente da appositi rulli per portarla poi in orizzontale, in continuo senza interruzione, teoricamente all’infinito (da cui il nome di colata continua).
Ci sono sei di queste billette che escono contemporaneamente da sei differenti bocche di uscita. Le billette vengono tagliate e trasferite alle laminazioni a caldo successive.
Ci sono due differenti linee di laminazione a caldo: una per la produzione di tondi nervati per reti elettrosaldate in barre o in rotoli, l’altra per la produzione di vergelle, dalla superficie liscia che verranno poi laminate a freddo.
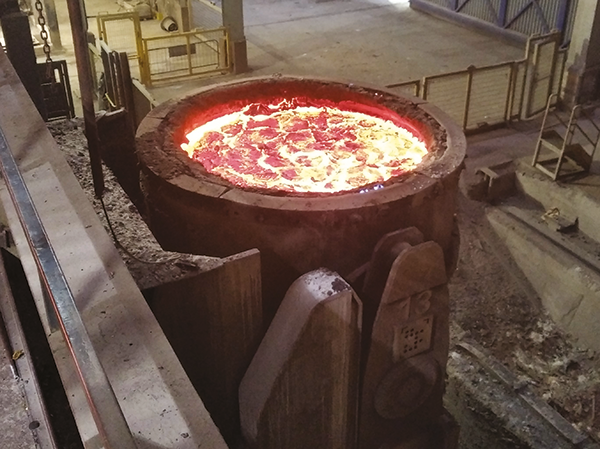
Il laminatoio del tondo per cemento armato in barre ed in rotoli è collegato direttamente con l’acciaieria attraverso un tunnel e via rulli che portano le billette già ad alta temperatura al forno di preriscaldo per raggiungere i 1200 C° necessari per la laminazione.
All’uscita dal forno di preriscaldo una saldatrice elettrica in linea salda tra loro le billette permettendo così una laminazione in continuo senza alcuna interruzione.
L’impianto è dotato di 20 gabbie di laminazione. La gamma produttiva va da 8 a 40 mm per il laminato in barre e da 10 a 32 mm per il laminato in rotoli.
L’altro laminatoio per la vergella è a 2 vie di laminazione e può laminare le billette fino ed una lunghezza di 16 m in una gamma di diametri da 5,5 a 21,5 mm. Dopo il forno di preriscaldo a gas che porta la temperatura della billetta a ca. 1200 C°.(le billette possono essere caricate nel forno anche a caldo provenienti direttamente dall’acciaieria), le billette passano attraverso treni di laminazione per un totale di 32 gabbie. Vengono raffreddate e condizionate. Segue il confezionamento del prodotto.
La vergella è destinata in gran parte ad altri reparti Pittini o ad altre aziende del Gruppo stesso, sia in Italia che all’estero per la produzione di laminati per diversi settori dell’industria meccanica per quanto riguarda l’acciaio a basso carbonio, mentre la vergella in acciaio ad alto carbonio è destinata all’edilizia con la produzione di rete elettrosaldata o tondo nervato in rotolo.
Tutti i reparti sono automatizzati, rispettano i requisiti dell’industria 4.0. Non si vede quasi personale in reparto, le sale controllo monitorano i processi, con personale giovane che scambiano informazioni tra di loro in friulano.
Il tour della fabbrica è durato quasi due ore e i partecipanti sono stati divisi in due gruppi. Non siamo riusciti a prendere nota dei nomi dei capi turno, che ci hanno accompagnato con le loro spiegazioni e che però ringraziamo. Come pure ringraziamo la gentilissima Romina Casasola, nostro riferimento durante la organizzazione, e il nostro collega Mario Ursella, ex Pittini, che ha fatto da facilitatore per il tutto. Come ringraziamento alla Pittini è stata consegnata una targa ricordo, immortalata con una foto.
24 maggio 2024