Ricarica intelligente delle batterie
La ricarica intelligente delle batterie per l'efficientamento energetico nella intra-logistica e nei trasporti è stato l'argomento della videoconferenza Progetto Innovazione di ALDAI Federmanager del 15 dicembre 2021
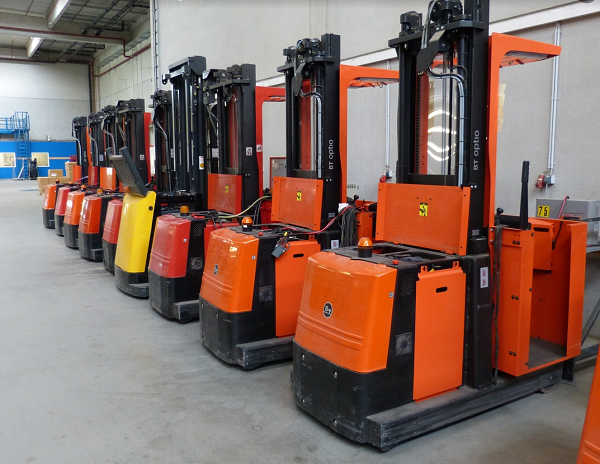
Photo by Pixabay
Domenico Arces
Associato Federmanager partecipante al progetto Sviluppo PMI, qualificato dal Digital Innovation Hub Lombardia per la valutazione delle opportunità della transizione digitale
Il Prof. Cappuccino, docente di Elettronica presso UNICAL – Università della Calabria – e CEO della startup CalBatt ha introdotto l’argomento sul risparmio energetico con una presentazione sulla “gestione della ricarica delle batterie”.
In particolare, è stato trattato il tema della vita delle batterie, in termini di cicli di carica e scarica, che dipende dalle modalità con cui tali cicli sono attuati.
Il prof. Cappuccino ha sintetizzato l’argomento prendendo ad esempio le ricariche dei carrelli elevatori e forklift, allargando il discorso ai veicoli elettrici in generale.
Partendo dallo sviluppo e dall’impiego che i forklift stanno avendo presso le aziende italiane per la movimentazione di carichi (più di 45000 unità vendute nel 2020), il relatore ha illustrato un’attenta analisi dei costi. Una macchina di medie dimensioni (48 V, 750 Ah) utilizzata per un turno al giorno per 5 giorni alla settimana ha un costo annuo di 3.945 € suddiviso in: consumo energia per 2.160 €/anno, manutenzione 185 €/anno e costo batteria di 1.600 €/anno.
Nel ciclo di ricarica di una batteria vi sono perdite ad ogni passaggio. Con i tradizionali sistemi si hanno perdite per effetto Joule, rispetto all’energia prelevata in rete, pari al 35% nell’unità di carica ed al 25% nella batteria.
Anche con sistemi più evoluti (ad es. inverter ad alta frequenza) tali perdite si riducono rispettivamente al 10% ed al 25% nella batteria. In questo caso, il costo totale annuo scende a 3.705 €. Il miglioramento è dovuto al minor prelievo di energia di rete che scende a 1.920 €/anno.
Nonostante la maggiore efficienza, anche nei sistemi più evoluti il riscaldamento elevato (cioè l’energia non accumulata e sprecata in calore) riduce notevolmente la vita della batteria. Questi sistemi, infatti, non tengono conto delle condizioni della batteria variabili da un istante all’altro, e completano l’ultima fase di carica con un over-charging.
L’innovazione della "ricarica intelligente" consiste in una tecnologia capace di rilevare in ogni istante i parametri di batteria e unità di carica, e di erogare la giusta potenza per evitare inutili perdite e danneggiamenti. Si tratta di un processo di carica dinamico che considera lo stato in cui si trova la batteria e ne adatta la ricarica. Anche il completamento nell’ultima fase di ricarica, praticamente non prevedibile, è monitorato ed ottimizzato in ogni istante evitando sprechi di energia.
In pratica, con riferimento al forklift considerato nell’esempio, questa innovazione consente di ridurre il riscaldamento di circa 3 °C e quindi le perdite nella batteria, aumentandone la vita utile del 25%. Il costo totale di esercizio si riduce sino a 2.936 €/anno.
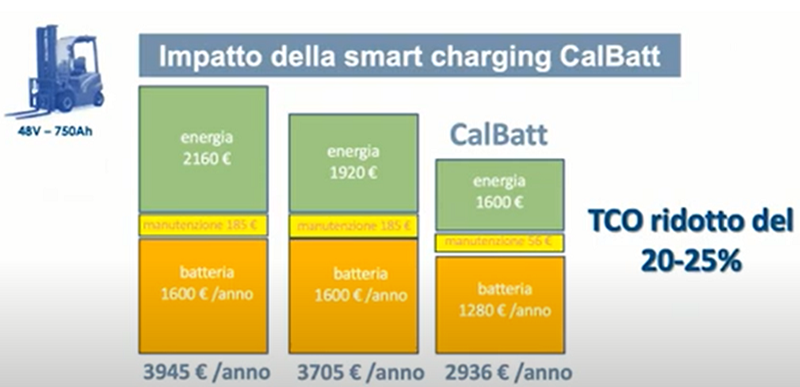
Da notare che, oltre al minor costo di energia e al maggior periodo di ammortamento della batteria, vi è anche un costo di manutenzione inferiore dovuto al minor riscaldamento ed alla minor frequenza di intervento per eseguire i rabbocchi necessari. Infatti, nell’ultima fase di carica, non sviluppandosi gas, è necessario un minore ripristino di elettrolita.
Tutto ciò gioca a vantaggio del risparmio energetico. Il relatore ha ricordato che attuare un risparmio di 5 MW corrisponde ad una riduzione di CO2 pari ad una tonnellata di petrolio equivalente.
Lo sviluppo effettuato presso la UNICAL ha generato l’attività della CalBatt, e diverse aziende in Italia ne hanno già tratto un vantaggio realizzando risparmi tra il 14 ed il 32% sulla componente energia.
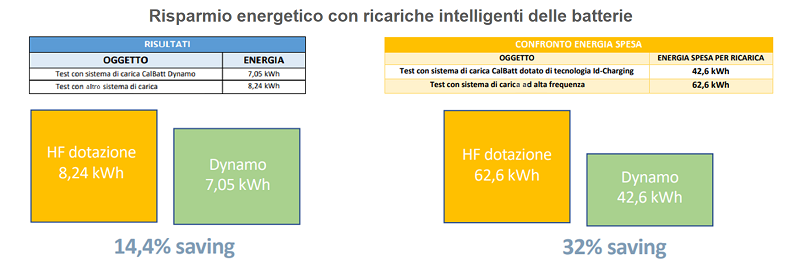
Per dare un’idea dei vantaggi offerti da una ricarica intelligente, è stato calcolato il beneficio ottenibile in un intervento di efficientamento della sala ricarica per una media impresa con un parco di 20 carrelli (15 retrattili e 5 frontali). Un tale intervento può consentire un risparmio annuale fino a poco meno di 26.000 €: di cui 17.500 € sui costi energetici e 8.300 € di risparmio sulle batterie. Su un arco temporale di 5 anni, questo significa avere un risparmio complessivo di quasi 130.000 €. Una chiara opportunità di riduzione costi di gestione e di rilancio della competitività delle imprese.
Oltre al risparmio energetico delle singole unità di ricarica, è molto importante l’odierna tendenza a gestire i picchi di energia richiesti ad esempio dai grandi centri logistici per la ricarica dei carrelli elevatori. In pratica si può distribuire il numero di unità da ricaricare in un arco temporale più ampio, dando priorità a quelle che riprenderanno il servizio per prime. Vi è però un metodo più intelligente, basato su una ricarica contemporanea di tutte le unità, che utilizza una potenza più bassa e massimizza l’efficacia. In pratica, quella che è una opportunità per un singolo carrello elevatore, può diventare un’opportunità per una intera flotta anche per più sedi dislocate sul territorio. Il sistema consiste nelle cosiddette unità di consumo abilitate virtuali, attraverso cui si possono aggregare virtualmente più carrelli in un’unica unità di assorbimento di energia. Tutto ciò permette al gestore della rete una riduzione dei picchi di erogazione e alle utenze una ulteriore opportunità di riduzione dei costi di gestione.
Oltre al mondo dei carrelli elevatori, questa tecnologia è già applicata nei trasporti urbani (come nell’esperienza del deposito ATM di S. Donato M.se). Nuovi sviluppi sono in corso su infrastrutture di ricarica di veicoli elettrici per le quali è disponibile il CIR (Controllore Infrastrutture di Ricarica), un apparecchio che rende intelligente l’unità Wallbox di ricarica domestica dell’autovettura. Il CIR permette, in determinate fasce orarie, il passaggio gratuito per l’utente da 3 a 6 KW di potenza erogata. In pratica, con una Wallbox completa di sistema CIR sarà gratuitamente concessa all’utente una potenza più alta per la ricarica del veicolo, ed il gestore potrà modulare dall’esterno la potenza erogata in caso di aumento dei carichi assorbiti.
Altro recente sviluppo è quello per lo Smart-Grid. Ad esempio, una cittadina in Puglia ha previsto sul sistema fotovoltaico comunale l’applicazione di batterie di accumulo gestite da una unità intelligente. L’energia accumulata è utilizzata per la ricarica dei veicoli elettrici di trasporto urbano. L’idea non è nuova, ma tutti i flussi energetici sono ottimizzati in rete mediante il sistema di caratterizzazione dinamica dei parametri delle unità di ricarica e delle batterie. Inoltre, dal punto di vista della sostenibilità ambientale, le batterie utilizzate in questo progetto sono batterie usate fornite dalla NISSAN dopo rientro dal campo per raggiunta capacità di ricarica dell’80%. Infatti, le batterie 2nd-Life, pur essendo ai limiti previsti per le vetture elettriche, possono essere utilizzate a terra per creare un accumulo di energia anziché essere smaltite. La residua capacità di carica di tali batterie è molto affidabile, proprio perché sono state utilizzate su vettura assolvendo alla loro funzione.
Di seguito le ulteriori considerazioni del prof. Cappuccino a conclusione dell’incontro.
L’industria dei carrelli elevatori, per rendere più veloci le ricariche, ha recentemente adottato la tecnologia delle batterie al litio, propria dell’industria automobilistica, in sostituzione di quelle al piombo. La ricarica veloce però, contribuisce a deteriorare più rapidamente le batterie.
Il saving sui costi realizzabile con l’applicazione di un sistema di ricarica intelligente è ovviamente proporzionale alla quantità di energia utilizzata. Per macchine poco energivore, il saving è modesto.
La riciclabilità delle batterie è pressoché totale. Quindi non avremo problemi legati al relativo smaltimento.
Il tema dell’incontro è stato interessante e condiviso dai partecipanti, non solo per gli aspetti tecnici spesso trascurati per le batterie, ma anche per i risvolti economici, sociali, ambientali e di sostenibilità.
Per scaricare la presentazione del Prof. Gregorio Cappuccino cliccare
Per il video dell'incontro cliccare l'immagine
01 gennaio 2022